Casting Aluminum 101: Crucial Steps for Newbies
Casting Aluminum 101: Crucial Steps for Newbies
Blog Article
Aluminum Casting Providers Unveiled: Necessary Insights and Tips
Exploring the world of aluminum casting services can unveil a globe of complex processes and nuanced factors to consider that are essential for successful results. As sectors increasingly transform to aluminum for its light-weight yet sturdy homes, comprehending the essentials of casting becomes paramount. From the fundamental methods to the detailed details that can make or break a casting project, there is a riches of insights and ideas waiting to be found. So, as we venture right into the realm of light weight aluminum casting solutions, prepare to discover the crucial elements that can form the trajectory of your tasks and elevate your understanding of this detailed craft.
The Essentials of Light Weight Aluminum Casting
What basic processes are included in aluminum casting that develop the foundation of this commonly used manufacturing method? Light weight aluminum casting is a cost-effective and flexible method utilized in various industries to create facility and intricate steel components. The process starts with the melting of aluminum ingots in a heating system, generally at temperatures varying from 1220 ° F to 1670 ° F, depending upon the details aluminum alloy being used. As soon as molten, the aluminum is put into a pre-designed mold dental caries, where it strengthens and takes the form of the mold.
Trick aspects such as mold layout, gating system, and cooling rate play an important duty in establishing the final quality of the actors aluminum part. The mold and mildew can be made of numerous products like financial investment, sand, or steel spreading wax, depending on the intricacy of the part and the preferred surface area finish. After solidification, the mold is gotten rid of, and the spreading undergoes finishing processes such as heat surface area, machining, and therapy layer to fulfill the needed requirements. Understanding these essential procedures is necessary for achieving premium light weight aluminum castings with mechanical residential properties and accurate measurements.
Different Casting Approaches Clarified
Exploring the different strategies used in aluminum casting uses valuable insights into the diverse techniques made use of to accomplish precise and detailed steel components. One usual approach is sand casting, where a mold and mildew is created making use of compacted sand around a pattern of the preferred part. One more approach, pass away casting, involves infusing liquified light weight aluminum right into a steel mold under high stress.
Factors to Consider When Picking a Service Provider
When picking a light weight aluminum casting provider, assessing their experience and proficiency is important for ensuring quality and dependability in the production procedure. The company's experience in the area indicates their knowledge with various casting techniques, potential difficulties, and finest practices. It is necessary to ask concerning the sorts of projects they have functioned on in the past, guaranteeing they line up with the complexity and specifications of your own task.
Furthermore, think about the provider's credibility within the sector. Look for testimonials, endorsements, and case research studies that show their capability to provide top quality light weight aluminum spreadings consistently. A reputable supplier will certainly commonly have qualifications or associations with industry companies, showcasing their commitment to excellence and adherence to market requirements.
Furthermore, analyze the provider's capabilities in regards to modification, quantity demands, and job timelines. Make certain that they can suit your certain demands and have the versatility to range manufacturing as required. Efficient interaction and openness regarding costs, preparation, and quality assurance procedures are also vital elements to consider when selecting an aluminum spreading company.
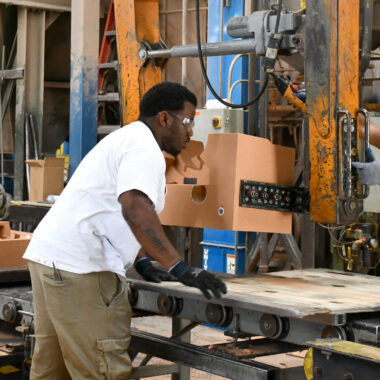
Common Obstacles and Solutions
Browsing via the complexities of light weight aluminum spreading processes usually presents producers with a collection of difficulties that call for innovative solutions to guarantee efficiency and high quality in production. One typical obstacle encountered in aluminum spreading is the formation of flaws such as porosity, shrinking, or additions due to incorrect mold layout or poor metal high quality.
One more challenge hinges on accomplishing exact dimensional precision, particularly for complex geometries. Variations in cooling rates, mold development, and material residential or commercial properties can bring about inconsistencies from the intended dimensions. go Carrying out sophisticated modern technologies like computer-aided style (CAD) and computer system numerical control (CNC) machining can improve precision and uniformity in light weight aluminum casting. Additionally, maintaining correct control over the melting and pouring processes is vital to stop concerns like getting too hot or irregular circulation of the molten steel - casting aluminum. By purchasing automation and real-time surveillance systems, manufacturers can boost process control and lessen variants, eventually boosting the total quality of light weight aluminum actors products.
Tips for Optimizing Your Casting Projects
To improve the effectiveness and high quality of your light weight aluminum casting projects, carrying out calculated optimization techniques is necessary. One key pointer for optimizing your casting jobs is to carefully develop the gating system. By making certain that the gating system is well-designed and effectively put, you can boost the circulation of molten aluminum and decrease the possibilities of problems in the final spreading. Furthermore, utilizing computer system simulations can help in assessing the flow and anticipating of steel during the casting process, enabling changes to be made before real production begins.
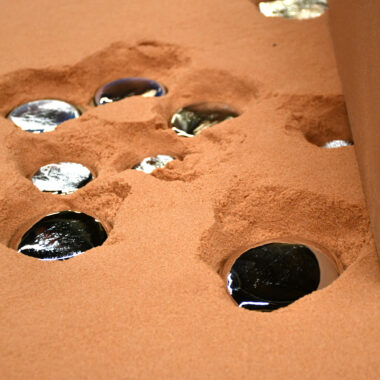
Verdict
In final thought, recognizing the essentials of light weight aluminum spreading, various casting methods, elements to think about when selecting a supplier, common see this page difficulties and options, and ideas for enhancing casting tasks are crucial for successful outcomes. By sticking to these understandings and executing ideal individuals, practices and services can ensure reliable and efficient light weight aluminum casting solutions that fulfill their particular requirements and demands.
Understanding these basic processes is vital for achieving top notch light weight aluminum spreadings with specific measurements and mechanical properties.
When selecting an aluminum spreading service supplier, view it assessing their experience and expertise is important for making sure top quality and reliability in the production process. Reliable communication and transparency relating to prices, lead times, and high quality control procedures are also critical elements to take into consideration when selecting an aluminum spreading service copyright.
Navigating with the complexities of aluminum spreading processes frequently provides suppliers with a collection of challenges that need innovative solutions to ensure performance and top quality in manufacturing. One common difficulty dealt with in light weight aluminum spreading is the formation of issues such as porosity, contraction, or inclusions due to incorrect mold style or insufficient steel quality.
Report this page